The Robot Revolution: Unleashing the Power of Industrial Automation
Industrial robots are rapidly transforming the manufacturing landscape, automating complex tasks and revolutionizing production processes.
Definition of Industrial Robot
An industrial robot is an autonomous, programmable machine capable of performing a variety of tasks in an industrial environment. These machines are typically used to enhance efficiency, precision, and safety in manufacturing operations.
1. Historical Origins and Evolution
- Industrial robots emerged in the 1950s, primarily used for welding and assembly tasks.
- Over the years, advancements in technology, such as microprocessors and computer vision systems, have significantly expanded their capabilities.
- Modern industrial robots are highly sophisticated machines that can perform a wide range of tasks with unparalleled precision and speed.
Humorous Story 1: The Robot Who Couldn't Weld
In a bustling factory, a newly installed welding robot caused havoc when it began welding everything in sight, including the workers' lunchboxes! Lesson learned: Ensure proper programming and safety measures before deploying robots.

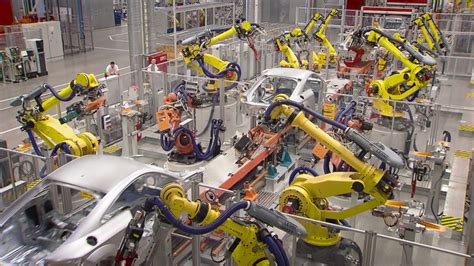
2. Types of Industrial Robots
-
Articulated robots: These robots have multiple joints, providing them with a wide range of motion. Ideal for welding, assembly, and material handling.
-
SCARA robots: SCARA (Selective Compliance Assembly Robot Arm) robots are designed for high-speed assembly tasks. They have a low profile and high precision.
-
Cylindrical robots: Cylindrical robots have a cylindrical reach, making them suitable for tasks such as loading and unloading.
-
Cartesian robots: These robots move in a Cartesian coordinate system, providing high precision and accuracy. Commonly used in painting and dispensing applications.
3. Applications in Manufacturing
-
Assembly: Robots perform tasks such as part placement, screw driving, and component assembly.
-
Welding: Industrial robots are used for various welding processes, including arc welding, spot welding, and laser welding.
-
Material handling: Robots automate the movement of materials throughout the manufacturing process, including loading, unloading, and palletizing.
-
Inspection and testing: Robots equipped with vision systems can inspect products for defects and perform quality control tests.
Humorous Story 2: The Robot That Painted Itself Blue
During a painting operation, a malfunctioning robot mistakenly painted itself blue instead of the parts it was supposed to paint. Lesson learned: Proper maintenance and regular calibration are crucial for robot reliability.
4. Benefits and Advantages
-
Increased production efficiency: Robots can work 24/7, reducing cycle times and increasing throughput.
-
Enhanced precision: Robots eliminate human error, resulting in consistent and high-quality products.
-
Improved safety: Robots perform dangerous tasks, reducing workplace accidents and injuries.
-
Cost reduction: Automation can significantly reduce labor costs, maintenance expenses, and overhead.
5. Design and Construction
-
Mechanical structure: Industrial robots are typically made of lightweight and durable materials, such as aluminum and carbon fiber.
-
Drivetrain: Robots use various types of drivetrains, including electric motors, hydraulic actuators, and pneumatic cylinders.
-
End-effectors: The end-effectors of robots are designed for specific tasks, such as welding torches, grippers, or spray nozzles.
Humorous Story 3: The Robot That Confused a Tool for a Toy
A playful robot accidentally mistook a cutting tool for a toy and began chasing a group of engineers around the factory. Lesson learned: Robots should be programmed with clear boundaries and safety protocols.
6. Programming and Control
-
Robot programming languages: Industrial robots are programmed using specialized languages, such as RobotC, VAL III, and KRL.
-
Control systems: Robots are controlled by microprocessors and software that interprets commands and manages their movements.
-
Simulation and offline programming: Advanced tools allow engineers to simulate robot operations and program them offline, reducing setup time and improving efficiency.
7. Safety Considerations
-
Risk assessment: A comprehensive risk assessment should be conducted before implementing industrial robots.
-
Safety features: Robots are equipped with various safety features, such as emergency stop buttons, light curtains, and collision detection sensors.
-
Training and education: Operators and maintainers should receive proper training on robot safety and procedures.
8. Current Trends and Future Directions
-
Collaborative robots: These robots work alongside human operators, providing assistance and enhancing productivity.
-
Artificial intelligence (AI) and machine learning: AI-enabled robots can learn from data and adapt to changing conditions.
-
Cloud-based robotics: Cloud connectivity allows robots to share data, receive updates, and collaborate remotely.
9. Impact on Employment
-
Job displacement: Automation can lead to job displacement, but it also creates new jobs in areas such as robot programming, maintenance, and data analysis.
-
Upskilling and retraining: Workers need to acquire new skills to adapt to the changing job market.
-
Government policies: Governments play a crucial role in supporting workers and ensuring a smooth transition to an automated future.
10. Ethical Considerations
-
Worker displacement: The potential for job displacement raises ethical concerns about the impact on workers and communities.
-
Safety and liability: Ensuring the safety and well-being of workers interacting with robots is paramount.
-
Responsibility and accountability: Determining responsibility and liability in cases of robot-related accidents is crucial.
Effective Strategies
-
Thorough planning and assessment: Conduct a detailed analysis of needs, objectives, and potential risks.
-
Phased implementation: Implement robots gradually to allow for adjustments and minimize disruption.
-
Training and support: Provide comprehensive training and support to operators, maintainers, and engineers.
-
Collaboration with experts: Consult with experienced professionals and industry experts for guidance and best practices.
Tips and Tricks
-
Define clear objectives: Identify specific goals and tasks for the robot to perform.
-
Optimize programming: Utilize advanced programming techniques to enhance robot efficiency and precision.
-
Regular maintenance: Establish a comprehensive maintenance schedule to ensure optimal performance and minimize downtime.
-
Monitor and evaluate: Track robot performance and make adjustments as needed to improve productivity and prevent issues.
Common Mistakes to Avoid
-
Underestimating safety risks: Fail to adequately assess and mitigate potential hazards associated with robot operations.
-
Overestimating capabilities: Assume robots can perform tasks beyond their capabilities, leading to frustration and production delays.
-
Lack of training: Neglect to provide proper training to operators and maintainers, resulting in errors and safety concerns.
-
Ignoring maintenance: Fail to perform regular maintenance, leading to premature equipment failure and costly repairs.
Potential Drawbacks
-
High upfront cost: Acquiring and implementing industrial robots can be a significant investment.
-
Job displacement concerns: Automation can lead to job losses in certain sectors.
-
Ethical considerations: The impact of robots on employment and society raises ethical questions that need to be addressed.
Pros and Cons
Pros:
- Increased efficiency and productivity
- Enhanced precision and quality
- Improved safety and reduced accidents
- Lower operating costs and increased profitability
Cons:
- High upfront investment
- Potential job displacement
- Requires specialized skills for programming and maintenance
- Ethical concerns about the impact on employment

Call to Action
Embracing industrial robots is crucial for businesses looking to enhance productivity, improve quality, and reduce costs. By carefully planning, implementing, and managing these machines, manufacturers can unlock the full potential of industrial automation and gain a competitive advantage in the global marketplace.
References
Tables
Table 1: Applications of Industrial Robots
Application |
Tasks |
Assembly |
Part placement, screw driving, component assembly |
Welding |
Arc welding, spot welding, laser welding |
Material handling |
Loading, unloading, palletizing |
Inspection and testing |
Defect inspection, quality control tests |
Table 2: Types of Industrial Robots
Type |
Characteristics |
Articulated |
Multiple joints, wide range of motion |
SCARA |
Low profile, high-speed assembly tasks |
Cylindrical |
Cylindrical reach, loading/unloading |
Cartesian |
Cartesian coordinate system, high precision |
Table 3: Benefits of Industrial Robots

Benefit |
Value |
Increased production efficiency |
Reduced cycle times, higher throughput |
Enhanced precision |
Consistent and high-quality products |
Improved safety |
Elimination of dangerous tasks |