Cap Liners: The Unsung Hero of Your Bottles
Introduction
Cap liners are unsung heroes that play a critical role in the packaging of beverages, pharmaceuticals, and personal care products. These thin but mighty components ensure product quality, safety, and shelf life.
Functions of Cap Liners
Cap liners serve multiple functions:
-
Provide a seal: They create an airtight and watertight seal between the bottle and the cap, preventing contamination and leakage.
-
Maintain product integrity: They protect the product from external factors such as oxygen, moisture, and light, preserving its potency and flavor.
-
Enhance product safety: They reduce the risk of tampering and prevent the introduction of foreign substances into the product.
-
Facilitate dispensing: They provide a controlled opening for dispensing the product, ensuring accurate dosing and preventing spillage.
Types of Cap Liners
Various types of cap liners are available, each designed for specific applications:
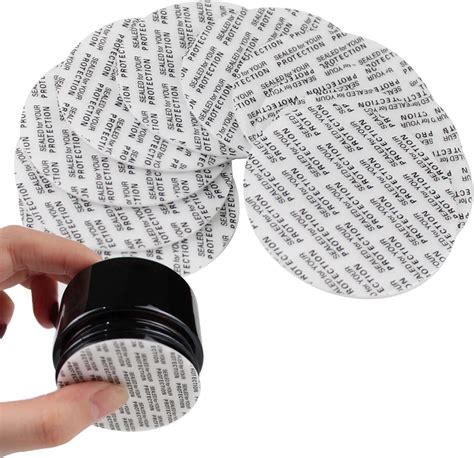
-
Pressure-sensitive liners: Adhere to the bottle opening without adhesive and are easy to remove.
-
Heat-seal liners: Require heat to bond to the bottle opening, providing a tamper-evident seal.
-
Induction seal liners: Create a hermetic seal by induction heating, which melts the liner and fuses it to the bottle.
-
Roll-on liners: Are crimped onto the bottle opening, providing a secure and tamper-proof seal.
Materials Used in Cap Liners
Cap liners are made from a variety of materials, including:
-
Aluminum: Provides excellent barrier properties against oxygen and moisture.
-
Polyethylene: Offers flexibility and is resistant to chemicals.
-
Teflon: Is non-stick and inert, making it ideal for sensitive products.
-
Rubber: Provides a tight seal and can withstand high temperatures.
Cap Liner Selection Criteria
Choosing the right cap liner involves considering several factors:
-
Product type: Different products require different levels of protection and barrier properties.
-
Packaging conditions: Factors such as temperature, humidity, and storage duration must be taken into account.
-
Dispensing requirements: The liner should facilitate easy and controlled product dispensing.
-
Cost: The cost of the liner should be balanced against its performance and value.
Benefits of Cap Liners
Cap liners offer numerous benefits:

-
Increased shelf life: They protect products from external factors, prolonging their shelf life.
-
Enhanced product quality: They prevent contamination and maintain product potency and flavor.
-
Improved safety: They reduce the risk of tampering and ensure product safety during storage and transportation.
-
Convenience: They facilitate easy and controlled dispensing, enhancing user experience.
Cap Liner Standards
Cap liners must meet specific standards and regulations to ensure their quality and performance. These standards include:
-
FDA compliance: Liners used for food and beverage packaging must comply with FDA regulations.
-
GMP guidelines: Liners for pharmaceutical applications must follow Good Manufacturing Practices (GMP) guidelines.
-
ISO certification: ISO-certified liners meet international standards for quality and safety.
Cap Liner Testing
Cap liners undergo rigorous testing to ensure their effectiveness and reliability. Tests include:

-
Seal integrity: Tests the liner's ability to prevent leakage and contamination.
-
Barrier properties: Evaluates the liner's resistance to oxygen, moisture, and light.
-
Tamper resistance: Verifies the liner's ability to detect and prevent tampering attempts.
-
Dispensing performance: Assesses the liner's ability to facilitate easy and accurate product dispensing.
Cap Liner Troubleshooting
Common issues with cap liners and their solutions:
-
Leakage: Ensure the liner is properly seated and the correct size for the bottle.
-
Difficulty dispensing: Check if the liner is damaged or has not been fully removed.
-
Tampering: Inspect the liner for any signs of manipulation or damage.
-
Product contamination: Investigate possible sources of contamination during packaging or storage.
Humorous Cap Liner Stories
Story 1: The Case of the Missing Liners
A beverage company discovered a batch of bottles without cap liners, resulting in massive product recalls. The investigation revealed that the liners had accidentally fallen into a batch of soda during production. The lesson learned: always double-check the presence of liners before bottling.
Story 2: The Sticky Surprise
A pharmaceutical company encountered a situation where their cap liners were sticking to the bottle openings. It turned out that the liners had been overcoated with adhesive, causing them to adhere too strongly. The solution: reevaluate the liner coating process to prevent excessive stickiness.
Story 3: The Tamper-Proof Puzzle
A cosmetics company faced a challenge with their tamper-proof cap liners. Customers complained that the liners were difficult to remove, even with the proper tools. The company realized that the liners had been over-crimped, making them too tight. The solution: adjust the crimping process to ensure tamper resistance without excessive force.
Conclusion
Cap liners are essential components that play a vital role in product packaging. By understanding their functions, types, and selection criteria, businesses can optimize their packaging operations and deliver high-quality products to their customers. Remember, the unsung hero of your bottles deserves proper attention and care.

Step-by-Step Approach to Cap Liner Selection
- Determine the product type and packaging conditions.
- Research different types of cap liners and their materials.
- Consider dispensing requirements and product compatibility.
- Evaluate cost and performance trade-offs.
- Choose a liner that meets standards and regulations.
- Conduct testing to verify the liner's effectiveness.
- Implement quality control measures to ensure consistent performance.
Potential Drawbacks of Cap Liners
-
Cost: Cap liners can add to packaging expenses, especially for premium materials.
-
Complexity: Some cap liners, such as induction seal liners, require specialized equipment and training for proper application.
-
Environmental concerns: Non-degradable liners can contribute to plastic waste.
-
Tampering: While cap liners can deter tampering, they cannot guarantee complete tamper-proof protection.
Frequently Asked Questions (FAQs)
Q: What is the most common type of cap liner?
A: Pressure-sensitive liners are the most widely used due to their ease of application and removal.
Q: How do I choose the right cap liner for my product?
A: Consider product type, packaging conditions, dispensing requirements, and cost when selecting a cap liner.
Q: Are cap liners required by law?
A: Cap liners are not mandatory by law but are recommended for product safety, quality, and shelf life.
Q: How often should I replace cap liners?
A: Replace cap liners after each use to ensure a proper seal and prevent contamination.
Q: What are the benefits of using cap liners?
A: Cap liners provide product protection, enhance quality, improve safety, and facilitate dispensing.
Q: What is the difference between induction seal liners and heat-seal liners?
A: Induction seal liners use heat generated by induction coils, while heat-seal liners require direct heat application to bond to the bottle.