The Robotic Revolution: Unveiling the Extraordinary Capabilities of Industrial Robots
Introduction
In the realm of modern manufacturing and automation, industrial robots have emerged as indispensable partners, transforming production lines and driving innovation across various industries. These sophisticated machines possess a remarkable set of caracteristicas de un robot industrial that empower them to perform complex tasks with precision, speed, and tireless consistency. In this comprehensive guide, we will delve into the intricate world of industrial robots, exploring their defining characteristics, uncovering their transformative potential, and outlining strategies for effective implementation.
Defining the Essence of an Industrial Robot
Industrial robots are programmable, automated machines designed to perform specific tasks in a variety of industrial settings. Unlike their counterparts in the realm of personal robotics, industrial robots are typically characterized by their:

-
Robust construction: Built to withstand the rigors of demanding industrial environments, industrial robots are constructed from durable materials that ensure longevity and reliability.
-
High precision and repeatability: Equipped with sophisticated sensors and control systems, industrial robots are capable of performing tasks with exceptional accuracy and consistency, minimizing errors and optimizing production efficiency.
-
Flexibility and programmability: Industrial robots can be programmed to perform a wide range of tasks, allowing them to adapt to changing production requirements and accommodate new applications.
-
Increased productivity: By automating repetitive and hazardous tasks, industrial robots enable manufacturers to increase production output, reduce labor costs, and enhance overall productivity.
Exploring the Versatile Applications of Industrial Robots
The caracteristicas de un robot industrial make them ideally suited for a diverse range of applications across various industries. From automotive manufacturing to electronics assembly, industrial robots are transforming production processes and driving innovation in sectors such as:
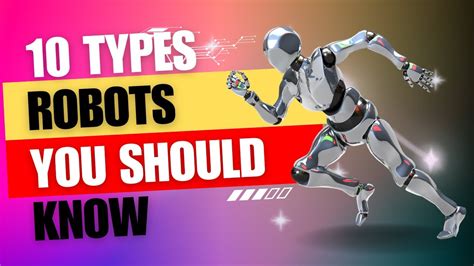
-
Automotive manufacturing: Industrial robots are extensively used in automotive assembly lines, performing tasks such as welding, painting, and component assembly with unmatched precision and speed.
-
Electronics assembly: In the intricate world of electronics manufacturing, industrial robots excel in tasks such as component placement, soldering, and testing, ensuring high-quality products and reducing production times.
-
Food and beverage processing: Industrial robots are employed in food and beverage processing facilities to automate tasks such as packaging, palletizing, and quality control, enhancing efficiency and ensuring food safety.
-
Healthcare: Industrial robots are making significant contributions to healthcare, assisting in surgical procedures, administering medications, and providing rehabilitation services with precision and accuracy.
-
Logistics and warehousing: In the realm of logistics and warehousing, industrial robots are used for tasks such as order fulfillment, inventory management, and package handling, optimizing operations and reducing labor costs.
Unveiling the Benefits of Industrial Robots: Redefining Efficiency and Innovation
The implementation of industrial robots offers a multitude of benefits for manufacturers, including:
-
Increased productivity: Industrial robots work tirelessly, 24 hours a day, 7 days a week, maximizing production output and reducing labor costs.
-
Improved quality: Industrial robots perform tasks with exceptional precision and repeatability, minimizing errors and enhancing product quality.
-
Enhanced safety: Industrial robots can perform hazardous and repetitive tasks, reducing the risk of accidents and injuries in the workplace.
-
Reduced costs: Industrial robots can significantly reduce labor costs, freeing up human workers to focus on more complex tasks.
-
Increased flexibility: Industrial robots can be easily reprogrammed to accommodate new tasks and product designs, providing manufacturers with greater flexibility and adaptability.
Mastering the Implementation of Industrial Robots: A Step-by-Step Guide
To successfully implement industrial robots in your facility, it is crucial to follow a systematic approach:
-
Identify the need: Determine the specific tasks or processes that would benefit from automation, considering factors such as cost savings, productivity gains, and safety improvements.
-
Research and select the right robot: Explore different types of industrial robots and their capabilities, considering factors such as payload capacity, reach, accuracy, and programming language.
-
Design the robot's workspace: Plan the robot's layout, including the necessary safety precautions, space requirements, and integration with existing equipment.
-
Install and program the robot: Physically install the robot and configure its programming to perform the desired tasks accurately and efficiently.
-
Train operators and maintenance personnel: Provide proper training to ensure that operators and maintenance personnel can safely and effectively operate and maintain the robot.
Embracing the Future: The Role of Industrial Robots in the Digital Revolution
As technology continues to advance, industrial robots are poised to play an increasingly pivotal role in the digital revolution, particularly in the context of:
-
Industry 4.0: Industrial robots are key components of Industry 4.0, a concept that emphasizes the integration of digital technologies and automation to drive manufacturing efficiency and innovation.
-
Artificial intelligence (AI): Industrial robots are becoming more sophisticated, incorporating AI capabilities to enhance their decision-making abilities, self-monitoring, and predictive maintenance.
-
Collaborative robotics: Industrial robots are evolving into collaborative partners, working alongside human workers in a shared workspace to optimize productivity and safety.
Common Mistakes to Avoid in Industrial Robot Implementation
To ensure the successful implementation and operation of industrial robots, it is essential to avoid common mistakes, such as:
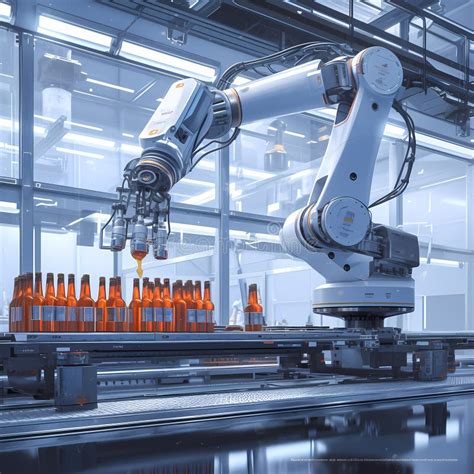
-
Underestimating the complexity of robot integration: Robotic integration involves multiple factors, including hardware, software, and safety considerations, which require careful planning and execution.
-
Lack of proper training: Inadequate training for operators and maintenance personnel can lead to safety hazards, reduced productivity, and increased downtime.
-
Neglecting safety measures: Failing to implement proper safety measures can pose risks to human workers and damage to equipment.
-
Insufficient maintenance: Regular maintenance is crucial to ensure the longevity, reliability, and optimal performance of industrial robots.
-
Overestimating the robot's capabilities: It is important to understand the limitations of industrial robots and avoid assigning tasks that are beyond their capabilities.
Inspiring Stories: Industrial Robots in the Limelight
1. The Robot that Saved the Day
In a bustling automotive assembly plant, a newly installed industrial robot experienced a minor glitch during a crucial welding operation. However, instead of halting production, the robot ingeniously detected the error and automatically adjusted its welding parameters, ensuring the seamless continuation of the assembly line. This remarkable incident highlighted the robot's advanced self-monitoring capabilities and its ability to adapt to unforeseen circumstances.
2. The Robot that Became an Artist
An industrial robot in an electronics manufacturing facility surprised its engineers by creating intricate patterns on the surface of electronic circuit boards during its downtime. The robot's unexpected artistic flair sparked a newfound appreciation for its precision and creativity, leading to the creation of a limited edition series of circuit boards featuring the robot's unique designs.
3. The Robot that Teaches a Lesson
In a warehouse setting, an industrial robot tasked with order fulfillment malfunctioned, causing a pileup of packages. Instead of panicking, the warehouse manager calmly approached the robot and discovered that it was simply overwhelmed by the sheer volume of orders. He realized that the robot needed additional time to process the instructions and adjusted the workflow accordingly. The incident taught the manager the importance of understanding the robot's limitations and adapting processes to maximize its efficiency.
Effective Strategies for Successful Industrial Robot Implementation
To harness the full potential of industrial robots, it is essential to implement effective strategies, such as:
-
Establish clear objectives: Define specific goals for robot implementation, such as increasing productivity or enhancing safety.
-
Conduct a thorough needs assessment: Determine the specific tasks and requirements that the robot will be responsible for.
-
Select the right robot: Consider factors such as payload capacity, reach, accuracy, and programming language when choosing the most suitable robot for your application.
-
Provide proper training: Train operators and maintenance personnel on the safe and efficient operation of the robot.
-
Implement rigorous maintenance: Establish a regular maintenance schedule to ensure the robot's longevity and optimal performance.
-
Monitor and evaluate performance: Continuously monitor the robot's performance and make adjustments as needed to maximize efficiency and productivity.
Case Studies: Quantifying the Impact of Industrial Robots
Numerous case studies have documented the benefits of industrial robots, providing tangible evidence of their transformative impact on various industries. For instance:
-
Automotive manufacturing: A leading automobile manufacturer implemented industrial robots in its assembly line, resulting in a 25% increase in productivity and a 10% reduction in labor costs.
-
Electronics assembly: A global electronics manufacturer deployed industrial robots in its production facility, leading to a 30% increase in product quality and a 15% reduction in production time.
-
Food and beverage processing: A major food and beverage company installed industrial robots in its packaging line, achieving a 20% increase in output and a 10% decrease in product damage.
Table 1: Defining Features of Industrial Robots
Feature |
Description |
Payload capacity |
The maximum weight that the robot can handle |
Reach |
The distance that the robot's arm can extend |
Accuracy |
The precision with which the robot can perform tasks |
Programming language |
The software used to instruct the robot |
Degrees of freedom |
The number of axes along which the robot can move |
Cost |
The investment required to purchase and maintain the robot |
Table 2: Applications of Industrial Robots
Industry |
Applications |
Automotive manufacturing |
Welding, painting, assembly |
Electronics assembly |
Component placement, soldering, testing |
Food and beverage processing |
Packaging, palletizing, quality control |
Healthcare |
Surgical assistance, medication administration, rehabilitation |
Logistics and warehousing |
Order fulfillment, inventory management, package handling |
Table 3: