Thrust Roller Bearings: A Comprehensive Guide to Design, Applications, and Maintenance
Thrust roller bearings are an essential component in various mechanical systems, playing a crucial role in transmitting axial loads. This comprehensive guide delves into the intricacies of thrust roller bearings, exploring their design, applications, and maintenance strategies.
Design of Thrust Roller Bearings
Types:
-
Spherical Roller Thrust Bearings: Capable of handling heavy axial loads and limited radial loads, these bearings feature spherical rollers that self-align within the bearing raceway.
-
Cylindrical Roller Thrust Bearings: Designed for high axial load capacities and precise axial displacement, these bearings utilize cylindrical rollers that are located between parallel raceways.
-
Tapered Roller Thrust Bearings: Employing tapered rollers that roll between tapered raceways, these bearings can withstand heavy axial loads and a combination of axial and radial loads.
Components:
-
Washer: The rotating component, located between the shaft and the housing, which carries the load-carrying rollers.
-
Raceway: The stationary component, which provides the rolling surface for the rollers.
-
Rollers: The cylindrical or spherical elements that transmit the axial load between the washer and raceway.
-
Cage: The component that separates and retains the rollers, preventing them from rubbing against each other.
Applications of Thrust Roller Bearings
Thrust roller bearings find applications in a wide array of industries, including:
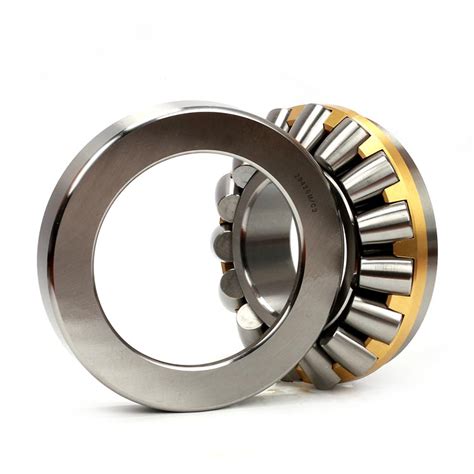

- Aerospace: For transmitting axial loads in aircraft engines, propellers, and landing gear.
- Automotive: Utilized in transmissions, differentials, and steering systems to handle axial forces.
- Construction equipment: Employed in excavators, cranes, and bulldozers to withstand heavy axial loads.
- Industrial machinery: Found in gearboxes, turbines, and pumps to manage axial forces and ensure precise axial positioning.
- Medical devices: Incorporated in surgical tools, dental drills, and MRI machines for precise and reliable motion control.
Maintenance Strategies
To ensure optimal performance and extend the service life of thrust roller bearings, proper maintenance is crucial:
-
Lubrication: Bearings should be lubricated regularly with high-quality oil or grease to minimize friction and wear.
-
Inspection: Periodic inspections of seals, bearings, and surrounding components help identify any potential issues or signs of wear.
-
Condition Monitoring: Vibration analysis, thermal imaging, and oil analysis techniques can provide early detection of potential failures.
-
Replacement: When bearings reach the end of their service life or become damaged, they should be promptly replaced to prevent catastrophic failures.
Effective Strategies for Thrust Roller Bearing Maintenance
1. Use High-Quality Lubricants: Select lubricants specifically designed for thrust roller bearings, ensuring they meet the required viscosity, temperature range, and load-carrying capacity.
2. Monitor Oil Levels and Condition: Regularly check oil levels and viscosity, and conduct oil analysis to detect contamination, degradation, or metal particles.
3. Maintain Proper Alignment: Ensure precise alignment between the bearing housing and shaft to prevent premature bearing failure.
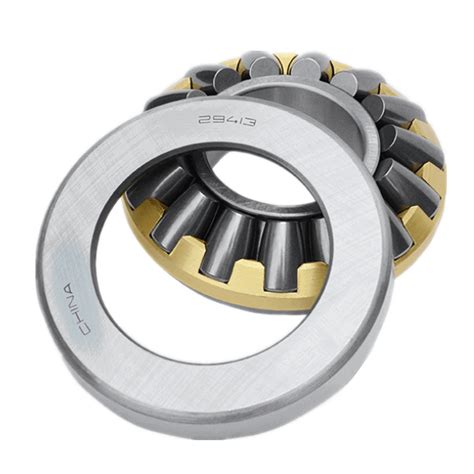
4. Control Bearing Loads: Avoid overloading bearings beyond their rated capacities, as excessive loads can lead to accelerated wear and damage.
5. Use Appropriate Seals: Utilize high-quality seals to prevent contamination and moisture ingress, which can adversely affect bearing performance.
Tips and Tricks for Thrust Roller Bearing Maintenance
-
Proper Handling and Storage: Handle bearings carefully using clean gloves to avoid contamination. Store them in a cool, dry place until installation.
-
Inspection Before Installation: Inspect bearings thoroughly for any damage or defects before mounting them.
-
Use Proper Assembly Tools: Employ appropriate tools and techniques during assembly to prevent bearing damage and ensure proper seating.
-
Grease Bearings Before Use: Apply a liberal amount of grease to the bearing prior to installation to reduce initial wear during start-up.
-
Follow Manufacturer Recommendations: Refer to the manufacturer's instructions for specific lubrication and maintenance intervals.
Common Mistakes to Avoid in Thrust Roller Bearing Maintenance
-
Overlubrication: Excessive lubrication can lead to churning and heat generation, potentially damaging the bearing.
-
Ignoring Oil Condition: Failure to monitor oil condition can result in contamination, leading to premature bearing failure.
-
Incorrect Bearing Mounting: Improper mounting can cause misalignment, resulting in increased bearing loads and premature wear.
-
Overloading Bearings: Exceeding bearing load capacities can shorten their service life significantly.
-
Neglecting Inspection and Monitoring: Lack of regular inspections and condition monitoring can prevent early detection of potential problems.
Step-by-Step Approach to Thrust Roller Bearing Maintenance
Step 1: Prepare and Gather Materials:
- Clean gloves
- Clean workbench
- Appropriate tools
- Lubricant
Step 2: Disassemble the Bearing:
- Remove the bearing housing or cover.
- Carefully extract the thrust roller bearing from its location.
Step 3: Inspect the Bearing:
- Examine the bearing for any signs of wear, damage, or contamination.
- Check the rollers, races, and cage for any imperfections or irregularities.
Step 4: Clean the Bearing:
- Use a clean solvent to remove any contaminants or old lubricant.
- Ensure all components are cleaned thoroughly.
Step 5: Lubricate the Bearing:
- Apply a generous amount of high-quality lubricant to the bearing surfaces.
- Distribute the lubricant evenly throughout the bearing.
Step 6: Reassemble the Bearing:

- Carefully position the thrust roller bearing into its housing or cover.
- Ensure the bearing is properly aligned and seated.
Step 7: Reinstall the Housing or Cover:
- Secure the bearing housing or cover back into place.
- Tighten the bolts or screws as per manufacturer's specifications.
FAQs on Thrust Roller Bearings
1. What are the advantages of using thrust roller bearings over other types of bearings?
Thrust roller bearings offer higher load capacities, reduced friction, and improved axial positioning precision compared to other bearing types.
2. How often should thrust roller bearings be lubricated?
Lubrication intervals depend on the bearing size, load, speed, and operating environment. Refer to the manufacturer's recommendations for specific lubrication schedules.
3. What are the signs of a failing thrust roller bearing?
Excessive noise, vibration, heat generation, and reduced axial load capacity indicate a potential bearing failure.
4. How can I extend the service life of thrust roller bearings?
Proper lubrication, regular inspections, condition monitoring, and avoiding overloading can significantly extend bearing service life.
5. What factors should be considered when selecting thrust roller bearings?
Load capacity, speed, alignment requirements, lubrication method, and operating environment are key factors to consider when selecting thrust roller bearings.
6. What are the most common applications for thrust roller bearings?
Thrust roller bearings are widely used in automotive, aerospace, construction, industrial machinery, and medical devices.
Conclusion
Thrust roller bearings play a critical role in a wide range of applications, transmitting axial loads with high efficiency and precision. By understanding their design, selecting appropriate maintenance strategies, and adhering to best practices, engineers and technicians can ensure optimal performance and extended service life of thrust roller bearings.