Needles for Bearings: A Comprehensive Guide
Needles for bearings, also known as needle rollers, are cylindrical rollers with a length that is typically 3 to 10 times their diameter. Their unique shape and small size make them ideal for applications where space is limited and high load-carrying capacity is required. Needles for bearings are widely used in various industries, including automotive, machinery, and aerospace.
Why Needles for Bearings Matter
Needles for bearings offer several advantages over traditional ball or roller bearings:
-
High Load Capacity: Their long and slender shape distributes loads over a larger surface area, leading to higher load-carrying capacity in both radial and axial directions.
-
Compact Size: Needles for bearings are significantly smaller than other types of bearings, allowing for more compact designs and saving space in applications where it is critical.
-
Low Friction: Their cylindrical shape and smooth surface minimize friction, resulting in lower energy losses and improved efficiency.
-
High Speed Capability: Needles for bearings can operate at higher speeds than traditional bearings due to their reduced centrifugal force.
-
Cost-Effective: Needles for bearings are relatively inexpensive to manufacture, making them a cost-effective solution for many applications.
Benefits of Using Needles for Bearings
The unique properties of needles for bearings offer several notable benefits:
-
Increased Load Capacity: By utilizing needles for bearings, engineers can significantly increase the load-carrying capacity of their designs without increasing the bearing size.
-
Reduced Friction and Wear: The low friction and smooth operation of needles for bearings result in reduced energy consumption, extended bearing life, and improved system efficiency.
-
Space Optimization: The compact size of needles for bearings allows for more efficient use of space, enabling the design of smaller and lighter systems.
-
Improved Speed Capabilities: Needles for bearings can handle higher operating speeds, allowing for more efficient and responsive systems.
-
Cost Savings: The cost-effectiveness of needles for bearings contributes to overall system cost savings, making them an attractive option for various applications.
Applications of Needles for Bearings
Needles for bearings are extensively used in a wide range of industries due to their unique advantages:

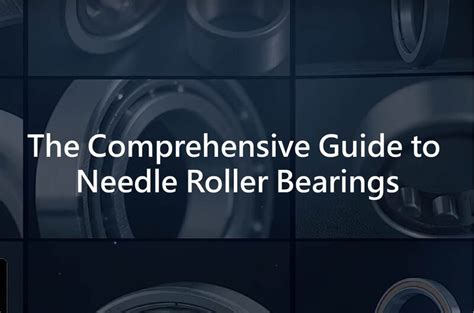
-
Automotive: Needles for bearings are commonly found in transmissions, engines, and steering systems, where they provide high load-carrying capacity and reduced friction.
-
Machinery: In industrial machinery, needles for bearings are used in gearboxes, conveyors, and rolling mills, where their compact size and high speed capability are crucial.
-
Aerospace: Needles for bearings play a vital role in aircraft engines, landing gear, and control systems, where reliability, high load capacity, and low weight are essential.
-
Medical: In medical devices such as surgical instruments and implantable devices, needles for bearings ensure precise movement and durability under demanding conditions.
Different Types of Needles for Bearings
Needles for bearings come in various types to meet specific application requirements:
-
Solid Needles: These needles consist of a single piece of hardened steel alloy, providing high load capacity and durability.
-
Caged Needles: Caged needles are held together by a cage or retainer, which maintains proper spacing and prevents misalignment.
-
Thin-Walled Needles: Thin-walled needles have a thinner cross-section, allowing for higher load capacity in limited space applications.
-
Drawn Needles: Drawn needles are manufactured by drawing cold-rolled steel through a series of dies, resulting in a smooth surface and enhanced fatigue strength.
Needle Bearings Assemblies
Needle bearings assemblies, also known as needle roller bearings, comprise needles for bearings arranged within a bearing race. These assemblies are typically used in applications where high radial loads and limited axial loads are encountered:

-
Drawn Cup Needle Roller Bearings: These bearings consist of a drawn cup outer race and a set of drawn needles contained within a cage. They are suitable for high radial loads and low to moderate axial loads.
-
Needle Thrust Bearings: Needle thrust bearings are designed to withstand axial loads and are commonly used in applications such as linear actuators and clutches.
Selection and Installation of Needles for Bearings
Proper selection and installation of needles for bearings are crucial for optimal performance and longevity:
-
Load Capacity: The load capacity of the needles for bearings should meet or exceed the expected operating loads to ensure reliability and durability.
-
Speed: Consider the operating speed of the application and select needles for bearings with appropriate speed ratings to avoid premature failure.
-
Lubrication: Needles for bearings require proper lubrication to reduce friction and wear. Consult the manufacturer's recommendations for the appropriate lubrication method and type.
-
Clearance: Proper clearance between the needles for bearings and the bearing race is essential to prevent binding and premature wear.
-
Orientation: Ensure that needles for bearings are installed in the correct orientation to withstand the expected loads.
Maintenance and Troubleshooting of Needles for Bearings
Regular maintenance and troubleshooting are crucial to ensure the longevity and proper functioning of needles for bearings:
-
Regular Lubrication: As mentioned earlier, proper lubrication is vital for reducing friction and wear. Follow the manufacturer's recommendations for lubrication intervals and methods.
-
Inspection: Periodically inspect needles for bearings for signs of wear, damage, or contamination. If any issues are detected, replace the bearings promptly.
-
Noise: Unusual noise during operation may indicate a problem with the needles for bearings. Investigate the source of the noise and address it immediately.
-
Vibration: Excessive vibration can be a sign of misalignment or improper installation. Check the alignment and installation of the needles for bearings and correct any issues.
Tips and Tricks for Using Needles for Bearings
- Use high-quality needles for bearings from reputable manufacturers to ensure reliability and longevity.
- Consider using caged needles for applications where precise spacing and alignment are critical.
- For high-speed applications, opt for needles for bearings with hardened steel alloys to enhance fatigue strength and durability.
- When space is constrained, thin-walled needles can provide a high load-carrying capacity within a limited cross-section.
- Ensure proper lubrication and follow the manufacturer's recommendations to minimize friction and wear.
FAQs on Needles for Bearings
1. What is the difference between solid and caged needles?
Solid needles are single pieces of hardened steel, while caged needles are held together by a cage or retainer. Caged needles provide more precise spacing and alignment, which is crucial for certain applications.
2. How do I choose the right needles for bearings for my application?
Consider the load capacity, speed, lubrication requirements, clearance, and orientation to select needles for bearings that meet your specific application needs.
3. How often should I lubricate needles for bearings?
The lubrication interval depends on the operating conditions and the manufacturer's recommendations. Regularly lubricate needles for bearings to minimize friction and wear.
4. What are the signs of worn or damaged needles for bearings?
Unusual noise, excessive vibration, and reduced performance can indicate worn or damaged needles for bearings. Inspect the bearings regularly and replace them if necessary.
5. How can I troubleshoot problems with needles for bearings?
Check for proper lubrication, inspect the bearings for damage, verify the alignment, and eliminate any potential sources of contamination.
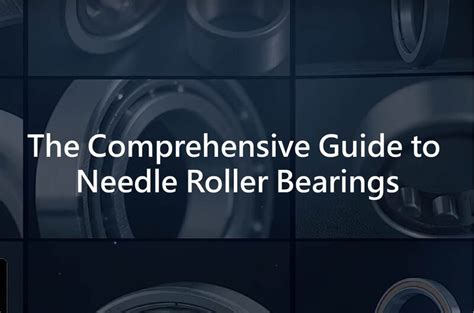
6. What industries commonly use needles for bearings?
Needles for bearings are widely used in automotive, machinery, aerospace, and medical industries.
Tables on Needles for Bearings
Type of Needle |
Advantages |
Applications |
Solid Needles |
- High load capacity - Durability - Suitable for heavy-duty applications |
- Transmissions - Engines - Steering systems |
Caged Needles |
- Precise spacing and alignment - Reduced friction - Suitable for high-speed applications |
- Gearboxes - Conveyors - Rolling mills |
Thin-Walled Needles |
- High load capacity in limited space - Reduced weight - Suitable for aerospace applications |
-Aircraft engines - Landing gear - Control systems |
Needle Bearing Assembly |
Advantages |
Applications |
Drawn Cup Needle Roller Bearings |
- High radial load capacity - Low to moderate axial loads - Suitable for space-constrained applications |
- Linear actuators - Clutches - Medical devices |
Needle Thrust Bearings |
- High axial load capacity - Low friction - Suitable for thrust load applications |
- Linear slides - Rotary tables - Gearboxes |
Parameter |
Considerations |
Importance |
Load Capacity |
- Calculate expected operating loads - Select needles for bearings with sufficient load rating |
- Ensures reliability and durability |
Speed |
- Determine operating speed - Choose needles for bearings with appropriate speed rating |
- Prevents premature failure |
Lubrication |
- Consult manufacturer's recommendations - Use appropriate lubrication method and type |
- Reduces friction and wear |
Clearance |
- Allow proper clearance between needles for bearings and bearing race |
- Prevents binding and premature wear |
Orientation |
- Install needles for bearings in the correct orientation |
-Withstands expected loads |