Ultrasonic Machining: A Comprehensive Guide to Advanced Material Removal
Ultrasonic machining (USM) is a non-traditional machining process that utilizes high-frequency ultrasonic vibrations to remove material from the workpiece. This innovative technique provides unparalleled precision and surface quality, making it ideal for machining hard, brittle, and complex materials that are difficult to process by conventional methods.
Principle of Ultrasonic Machining
USM employs a transducer to convert electrical energy into high-frequency mechanical vibrations. These vibrations are then transmitted to a cutting tool, typically made of a hard abrasive material, such as diamond or cubic boron nitride (CBN). The tool oscillates at frequencies ranging from 20 to 40 kHz, creating a rapid impact between the tool and the workpiece.
The impact generates high-pressure shock waves that break down the workpiece material at the microscopic level. The abrasive particles in the cutting fluid remove the disintegrated material, resulting in precise material removal.
Applications of Ultrasonic Machining
USM finds applications in various industries, including:
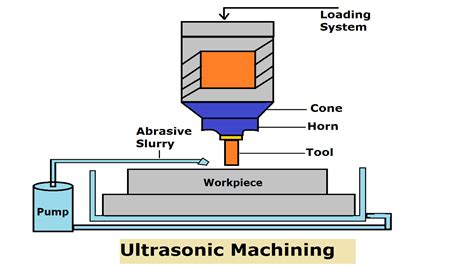
-
Medical: Manufacturing of surgical instruments, dental drills, and pacemakers
-
Aerospace: Production of fuel injector nozzles, turbine blades, and composite components
-
Electronics: Fabrication of printed circuit boards, sensors, and microchips
-
Jewelry: Engraving and cutting of precious metals and gemstones
-
Automotive: Machining of complex engine components, transmission gears, and fuel pumps
Advantages of Ultrasonic Machining
-
High precision: USM provides unmatched precision, with machining accuracy up to 0.001 mm. This makes it suitable for intricate machining operations.
-
Excellent surface quality: The non-contact nature of USM eliminates burrs and tool marks, resulting in a smooth and high-quality surface finish.
-
Machinability of hard and brittle materials: USM can effectively machine materials that are too hard or brittle for conventional machining processes, such as ceramics, glass, and composites.
-
Minimal heat generation: Ultrasonic vibrations generate minimal heat, preventing thermal damage to the workpiece.
-
Versatility: USM can be used to perform various operations, including drilling, milling, and engraving.
Challenges of Ultrasonic Machining
- ** Tool wear:** Abrasive particles can lead to tool wear, reducing machining efficiency and accuracy.
- ** Vibration isolation:** High-frequency vibrations can cause structural damage if not properly isolated.
- ** Fluid contamination:** The cutting fluid must be clean, as contaminants can clog the process and damage the workpiece.
- ** High energy consumption:** USM requires significant electrical energy to generate ultrasonic vibrations.
Tables
Table 1: Typical USM Parameters
Parameter |
Range |
Unit |
Frequency |
20-40 |
kHz |
Amplitude |
10-50 |
µm |
Cutting force |
1-10 |
N |
Cutting speed |
1-10 |
mm/s |
Table 2: Material Removal Rates for Different Materials
Material |
Removal Rate |
Unit |
Steel |
0.2-1 |
mm³/min |
Ceramics |
0.05-0.5 |
mm³/min |
Glass |
0.1-0.8 |
mm³/min |
Table 3: Comparison of USM with Conventional Machining

Feature |
USM |
Conventional Machining |
Precision |
High (0.001 mm) |
Medium (0.01 mm) |
Surface finish |
Excellent (no burrs) |
Good (some burrs) |
Material removal rate |
Low (few mm³/min) |
High (several cm³/min) |
Heat generation |
Minimal |
Significant |
Tool life |
Limited |
Long |
Step-by-Step Approach to Ultrasonic Machining
-
Material selection: Choose a compatible material with the required machinability characteristics.
-
Workpiece preparation: Clean and secure the workpiece in a suitable fixture.
-
Abrasive slurry preparation: Mix abrasive particles with a suitable cutting fluid to form a slurry.
-
Machine setup: Install the cutting tool and configure the machine parameters based on the workpiece material and removal rate.
-
Machining: Start the machining process and monitor the progress using sensors or optical equipment.
-
Tool maintenance: Regularly inspect and maintain the cutting tool to ensure optimal performance.
-
Post-processing: Clean the workpiece and perform any necessary post-processing operations, such as polishing or heat treatment.
Tips and Tricks
- Use a high-quality cutting fluid with a suitable viscosity and pH to enhance machining efficiency.
- Select the appropriate abrasive particle size based on the workpiece material and desired surface finish.
- Optimize machine parameters (frequency, amplitude, cutting force) through experimentation to achieve maximum material removal rate and surface quality.
- Ensure proper vibration isolation to prevent structural damage and improve machining accuracy.
- Regularly clean the cutting fluid and filters to minimize contamination and wear.
Common Mistakes to Avoid
-
Insufficient vibration isolation: This can lead to excessive vibration, machine damage, and reduced machining precision.
-
Contaminated cutting fluid: Contaminants can clog the process, damage the workpiece, and reduce tool life.
-
Improper abrasive selection: Using coarse abrasives for delicate materials can cause excessive material removal and poor surface finish.
-
Excessive cutting force: This can result in chipping and tool breakage, especially when machining brittle materials.
-
Neglecting tool maintenance: Ignoring tool maintenance can reduce machining efficiency and compromise the surface quality.
Conclusion
Ultrasonic machining is an innovative and versatile process that enables the precision machining of hard, brittle, and complex materials. By understanding the principle, applications, advantages, and challenges of USM, manufacturers can effectively utilize this technology to produce high-quality components for various industries. By following the step-by-step approach, employing tips and tricks, and avoiding common mistakes, industries can maximize the benefits of USM and create precise and intricate products.