Thrust Washers: An Essential Guide to Their Functions, Applications, and Maintenance
Thrust washers are unsung heroes in the mechanical world, playing a crucial role in preventing friction, protecting critical components, and ensuring smooth operation of machinery. Their humble appearance belies their significant impact on the performance and longevity of mechanical systems. This comprehensive guide will delve into the intricacies of thrust washers, exploring their functions, applications, and essential maintenance practices.
Functions of Thrust Washers
Thrust washers serve two primary functions:
-
Reducing Friction: Thrust washers are designed to minimize friction between two surfaces that experience axial loads. They act as a barrier between the surfaces, preventing direct contact and thereby reducing wear and tear.
-
Distributing Loads: Thrust washers distribute axial loads evenly across a larger surface area, reducing stress concentrations and preventing damage to the contacting surfaces.
Types of Thrust Washers
Thrust washers can be classified into several types based on their shape, material, and application:
-
Flat Washers: The simplest type of thrust washer, flat washers are thin, circular discs that fit between two parallel surfaces.
-
Tapered Washers: These washers have a tapered profile, allowing them to compensate for misalignment or angularity between the mating surfaces.
-
Thrust Plates: Thrust plates are larger, more robust thrust washers used in heavy-duty applications, such as engines and gearboxes.
Materials Used in Thrust Washers
The material of thrust washers is critical to their performance and durability. Common materials include:
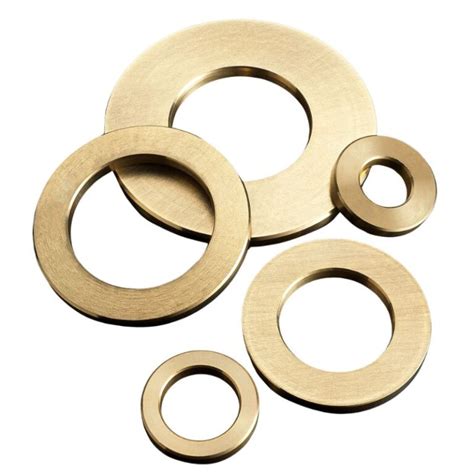
-
Steel: Steel thrust washers offer high strength and wear resistance, making them suitable for demanding applications.
-
Bronze: Bronze thrust washers have excellent bearing properties, low friction, and good corrosion resistance.
-
Polymer: Polymer thrust washers provide high wear resistance, electrical insulation, and the ability to operate in extreme temperatures.
Maintenance of Thrust Washers
Proper maintenance is essential for ensuring the longevity and effectiveness of thrust washers. Regular maintenance includes:
-
Inspection: Periodically inspect thrust washers for wear, damage, or corrosion. Replace washers if necessary.
-
Lubrication: Apply appropriate lubrication to the contact surfaces of thrust washers to reduce friction and extend their lifespan.
-
Adjustment: In some applications, thrust washers may require adjustment to ensure proper load distribution and alignment.
Applications of Thrust Washers
Thrust washers find applications in numerous industries and applications, including:


-
Automotive: Thrust washers are used in engines, transmissions, and differentials to reduce friction and protect critical components.
-
Industrial Machinery: In industrial machinery, thrust washers are employed in pumps, compressors, and gearboxes to ensure smooth operation and extend the lifespan of rotating parts.
-
Aerospace and Defense: Thrust washers are essential for high-performance aircraft and defense systems, where reliable operation is paramount.
-
Medical devices: Thrust washers are used in medical implants and surgical robots to minimize friction and protect delicate components.
Case Studies
Case Study 1: Failure Due to Inadequate Lubrication
In a manufacturing facility, a conveyor belt experienced premature failure due to a lack of lubrication on the thrust washer. The resulting high friction caused rapid wear and overheating of the washer, leading to its failure and the subsequent breakdown of the conveyor system.
Lesson Learned: Regular lubrication is critical for preventing thrust washer failures and ensuring smooth operation of machinery.
Case Study 2: Corrosion-Related Failure
A marine engine suffered a catastrophic failure when a thrust washer corroded and seized up. The corrosion was caused by exposure to saltwater, which penetrated the washer's protective coating. The resulting friction generated excessive heat, melting the washer and causing extensive damage to the engine.

Lesson Learned: Using thrust washers made of corrosion-resistant materials and providing adequate protection against harsh environmental conditions is essential for preventing premature failure.
Case Study 3: Success with Regular Maintenance
A power plant implemented a comprehensive maintenance program that included regular inspection and lubrication of thrust washers. As a result, the plant experienced a significant reduction in thrust washer failures and an increase in the lifespan of its critical machinery.
Lesson Learned: Adhering to a proactive maintenance schedule can prevent thrust washer failures, reduce downtime, and extend the lifespan of machinery.
Effective Strategies
To ensure the reliability and longevity of thrust washers, implement the following strategies:
-
Use High-Quality Materials: Select thrust washers made of high-strength, wear-resistant materials that are appropriate for the specific application and operating conditions.
-
Provide Adequate Lubrication: Apply the recommended lubricant to the contact surfaces of thrust washers to reduce friction and prevent wear. Choose the correct lubricant for the operating temperature, load, and environment.
-
Monitor Washer Condition: Regularly inspect thrust washers for wear, damage, or corrosion. Replace washers when they reach the end of their service life or show signs of distress.
-
Consider Coatings: Apply protective coatings to thrust washers to enhance their corrosion resistance and extend their lifespan in harsh environments.
-
Follow OEM Recommendations: Refer to the manufacturer's instructions when selecting, installing, and maintaining thrust washers. Failure to do so may compromise the performance and safety of the equipment.
Tips and Tricks
-
Avoid Overtightening: When installing thrust washers, avoid overtightening the bolts or screws. Excessive torque can warp the washer and reduce its effectiveness.
-
Use Alignment Tools: To ensure proper alignment of thrust washers, use alignment tools such as dowel pins or alignment shafts.
-
Check for Flatness: Before installing thrust washers, inspect them for flatness. Non-flat washers can lead to uneven load distribution and premature failure.
-
Use a Washer Stack: In applications with high axial loads, consider using a stack of thrust washers to distribute the load more evenly.
-
Consider Temperature Limits: Pay attention to the temperature limits of thrust washers. Operating them beyond their specified temperature range can lead to premature failure.
Call to Action
Thrust washers play a vital role in the smooth operation and longevity of mechanical systems. By understanding their functions, choosing the right materials, implementing effective maintenance practices, and following the tips and tricks outlined in this guide, you can maximize the performance and reliability of your machinery. Remember, regular inspection, proper lubrication, and appropriate installation are essential for keeping thrust washers in optimal condition and preventing costly breakdowns.