Thrust Washers: The Ultimate Guide to Functions, Applications, and Maintenance
Thrust washers, the unsung heroes of mechanical systems, play a crucial role in reducing friction and wear between rotating surfaces. This comprehensive treatise delves into the intricacies of thrust washers, providing valuable insights into their functions, applications, types, materials, and maintenance practices. Embark on this educational journey to empower yourself with the knowledge and expertise to optimize the performance and longevity of your mechanical systems.
Functions and Applications of Thrust Washers
Thrust washers serve a vital function in preventing the direct contact of rotating surfaces, thereby reducing friction and protecting the components from damage. They are employed in a wide array of industrial and automotive applications, including:
-
Automotive Engines: Thrust washers are essential in crankshaft and camshaft assemblies, where they prevent axial movement and control endplay.
-
Transmission Systems: Thrust washers are crucial in gearboxes and transmission shafts, mitigating axial forces and preventing gear damage.
-
Radial Bearings: Thrust washers are incorporated into radial bearings to withstand axial loads and enhance bearing stability.
-
Pump and Compressor Systems: Thrust washers play a vital role in pumps and compressors, preventing the axial movement of impellers and shafts.
-
Aerospace Engineering: Thrust washers are critical components in aircraft engines and landing gear systems, ensuring reliable operation under extreme conditions.
Types of Thrust Washers
Various types of thrust washers exist, each tailored to specific applications. These include:
-
Flat Thrust Washers: The most basic type, featuring a flat, circular design that is commonly used in low-load and low-speed applications.
-
Tapered Thrust Washers: Designed with a tapered profile, they provide a self-aligning action, compensating for misalignment and reducing friction.
-
Stepped Thrust Washers: Boast a stepped design, allowing for adjustment to accommodate different axial clearances.
-
Spherical Thrust Washers: Possess a spherical shape, offering self-alignment capabilities and increased load capacity.
-
Angular Contact Thrust Washers: Feature an angular contact surface, providing high axial load capacity and reduced friction.
Materials Used in Thrust Washers
The material selection for thrust washers is paramount to ensure optimal performance and durability. Common materials include:
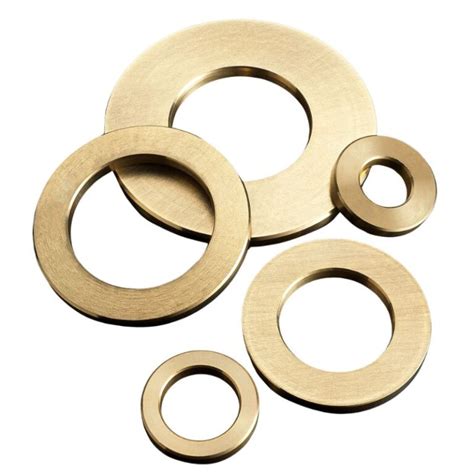
-
Steel: Offers excellent strength and wear resistance, but can generate noise and vibration.
-
Bronze: Provides a low-friction surface, but is less durable than steel.
-
PTFE: Exhibits excellent friction-reducing properties, but has limited load-carrying capacity.
-
Composite Materials: Combine the strengths of multiple materials, offering superior performance characteristics.
Maintenance of Thrust Washers
Regular maintenance is critical to extend the life of thrust washers and ensure optimal system performance. Key maintenance practices include:
-
Periodic Inspection: Visually inspect thrust washers for signs of wear, damage, or contamination.
-
Replacement: Replace thrust washers when they reach their wear limit or exhibit significant damage.
-
Lubrication: Lubricate thrust washers according to manufacturer recommendations to minimize friction and prevent premature wear.
-
Cleaning: Remove debris and contamination from thrust washers by cleaning them with appropriate solvents.
Effective Strategies for Optimizing Thrust Washer Performance
Implementing effective strategies can enhance thrust washer performance and extend their lifespan. These strategies include:

-
Selecting the Right Type and Material: Choose the appropriate thrust washer type and material based on the specific application requirements.
-
Ensuring Proper Installation: Install thrust washers correctly to prevent misalignment and premature wear.
-
Avoiding Overloading: Operate thrust washers within their rated load capacity to prevent excessive wear and damage.
-
Monitoring Temperature: Monitor operating temperatures to ensure that they do not exceed the material's limits.
-
Using High-Quality Lubricants: Employ high-quality lubricants recommended by the manufacturer to minimize friction and extend thrust washer life.
Tips and Tricks for Thrust Washer Maintenance
Implement these handy tips and tricks to maintain thrust washers effectively:
- Use a flashlight to inspect thrust washers for wear and damage in hard-to-reach areas.
- Clean thrust washers using a soft brush or cloth to avoid scratching or damaging the surface.
- Store thrust washers in a dry and clean environment to prevent corrosion and contamination.
- Consider using thrust washer wear indicators to monitor wear and determine the optimal replacement time.
Step-by-Step Approach to Thrust Washer Replacement
Follow these steps to replace thrust washers safely and efficiently:

-
Disassemble the System: Remove the components that provide access to the thrust washers.
-
Inspect the Thrust Washers: Examine the thrust washers for wear, damage, or contamination.
-
Remove the Old Thrust Washers: Carefully remove the old thrust washers using appropriate tools.
-
Clean the Contact Surfaces: Clean the contact surfaces where the thrust washers sit to remove debris and contamination.
-
Install the New Thrust Washers: Insert the new thrust washers into the correct position, ensuring proper alignment.
-
Reassemble the System: Reinstall the components that were removed to access the thrust washers, ensuring correct assembly.
Frequently Asked Questions (FAQs)
Q1: What are the common materials used in thrust washers?
A1: Common materials include steel, bronze, PTFE, and composite materials.
Q2: What factors determine the selection of a thrust washer?
A2: Application requirements, load capacity, speed, and environmental conditions influence the selection process.
Q3: How do you maintain thrust washers effectively?
A3: Implement regular inspections, lubrication, cleaning, and monitoring to extend thrust washer life.
Q4: What are the consequences of neglecting thrust washer maintenance?
A4: Neglect can lead to premature wear, damage, and reduced system efficiency.
Q5: When should thrust washers be replaced?
A5: Replace thrust washers when they reach their wear limit, exhibit damage, or fail to perform adequately.
Q6: How do thrust washers contribute to system efficiency?
A6: Thrust washers reduce friction between rotating surfaces, minimizing energy loss and enhancing system efficiency.
Conclusion
Thrust washers play a critical role in enhancing the performance and longevity of mechanical systems. Understanding their functions, applications, types, materials, and maintenance practices is essential for maximizing thrust washer effectiveness. Implement the strategies and tips outlined in this article to optimize thrust washer performance, extend their lifespan, and ensure the smooth and efficient operation of your mechanical systems. By embracing the knowledge and expertise presented here, you will empower yourself as a knowledgeable and effective professional in the field of mechanical engineering.
