The Ultimate Guide to Thrust Washers: A Comprehensive Resource for Engineers
Introduction
Thrust washers are critical components in various mechanical systems, providing support and reducing friction between rotating surfaces. Understanding their function, types, materials, and applications is crucial for engineers designing and maintaining machinery.
What is a Thrust Washer?
A thrust washer is a thin, ring-shaped bearing that withstands axial loads (forces acting perpendicular to the surface). It is positioned between two rotating or sliding surfaces to prevent metal-to-metal contact and reduce friction.
Functions of Thrust Washers
-
Load Bearing: Supports axial loads between rotating surfaces, distributing them evenly.
-
Friction Reduction: Provides a sliding surface between components, minimizing friction and wear.
-
Alignment: Ensures proper alignment of rotating elements, preventing misalignment and excessive stress.
Types of Thrust Washers
Thrust washers come in various types, each tailored to specific applications:
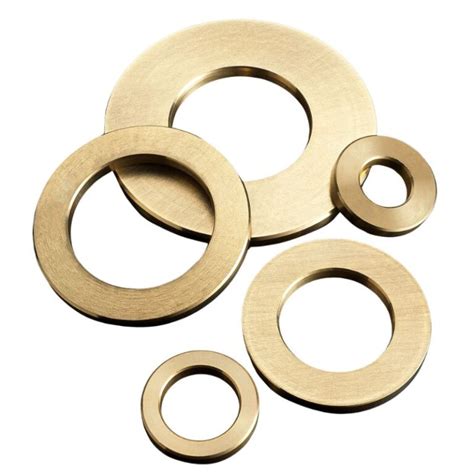
-
Plain Washers: Simple, flat discs without any special features. Suitable for low load and speed applications.
-
Tapered Washers: Feature a tapered inner or outer diameter, guiding components into alignment.
-
Flanged Washers: Have a raised flange on one or both sides, preventing axial movement.
-
Spherical Washers: Possess a concave or convex surface, accommodating misalignments and axial loads.
-
Ball Thrust Washers: Contain hardened steel balls between two hardened races, allowing high-speed operation and withstanding heavy loads.
Materials for Thrust Washers
The material choice for thrust washers depends on the operating conditions:
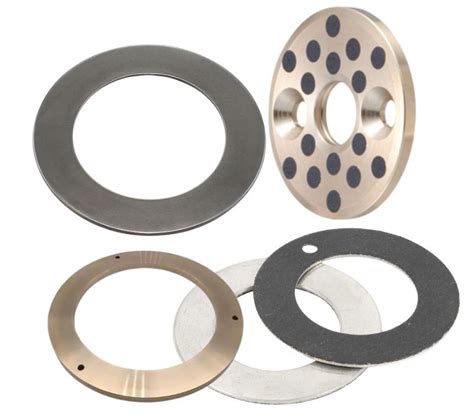
-
Steel: Suitable for general-purpose applications, offering strength and durability.
-
Bronze: Provides low friction and is commonly used in high-temperature and high-pressure environments.
-
PTFE (Teflon): Non-metallic материал with excellent friction reduction properties and chemical resistance.
-
Nylon: Lightweight and resilient, suitable for low-load and high-speed applications.
-
Composite Materials: Combine different materials to achieve specific properties, such as high strength and low friction.
Applications of Thrust Washers
Thrust washers find applications in a wide range of industries, including:
-
Automotive: Transmissions, differentials, and engine bearings.
-
Industrial Machinery: Pumps, compressors, and gearboxes.
-
Aerospace: Jet engines, propellers, and landing gear.
-
Construction Equipment: Cranes, excavators, and bulldozers.
-
Household Appliances: Washing machines, refrigerators, and dryers.
Importance of Thrust Washers
Thrust washers are essential for mechanical systems for several reasons:
-
Load Capacity: They provide reliable support for axial loads, preventing component failures.
-
Friction Reduction: By minimizing friction, thrust washers improve efficiency, reduce wear, and extend component life.
-
Alignment: They ensure proper alignment of rotating surfaces, preventing misalignment and premature wear.
-
Vibration Damping: Some thrust washers are designed to absorb vibrations, reducing noise and vibration levels.
Benefits of Using Thrust Washers
The benefits of using thrust washers in mechanical systems include:

-
Increased Efficiency: Reduced friction enhances efficiency and lowers energy consumption.
-
Extended Component Life: Reduced wear and tear prolongs the lifespan of components.
-
Improved Performance: Proper alignment and load distribution optimize system performance.
-
Lower Maintenance Costs: Reduced friction and wear minimize the need for frequent maintenance and repairs.
-
Increased Safety: Preventing component failures due to excessive loads or misalignment improves safety.
Common Mistakes to Avoid
-
Using Improper Size or Type: Selecting a thrust washer with the incorrect size or type can lead to premature failure or reduced performance.
-
Overloading: Exceeding the rated load capacity of a thrust washer can cause deformation or failure.
-
Incorrect Installation: Improper installation, such as not using proper alignment tools or torquing to the specified value, can result in premature wear or misalignment.
-
Neglecting Maintenance: Regular inspection and replacement of thrust washers as needed is crucial to prevent failures and maintain optimal performance.
-
Ignoring Environmental Conditions: Thrust washers made from inappropriate materials for the operating environment can fail prematurely due to corrosion, wear, or temperature limitations.
Effective Strategies for Selecting and Using Thrust Washers
-
Determine Loads and Conditions: Calculate the specific axial loads and operating conditions to select the optimal thrust washer type and material.
-
Consult with a Supplier: Seek guidance from knowledgeable suppliers to identify the most appropriate thrust washer for the application.
-
Proper Installation: Follow established installation procedures to ensure correct alignment and avoid premature failures.
-
Regular Maintenance: Implement a consistent inspection and maintenance schedule to monitor thrust washer condition and replace them as necessary.
-
Consider Advanced Materials: Explore the use of advanced materials or coatings to enhance performance and durability in demanding applications.
Tips and Tricks for Optimizing Thrust Washer Performance
-
Use Flanged Washers: Flanged washers prevent axial movement, reducing the risk of misalignment and excessive loads.
-
Consider Spherical Washers: Spherical washers accommodate slight misalignments, reducing stress and wear.
-
Lubricate Regularly: Lubrication minimizes friction and wear, extending thrust washer lifespan.
-
Monitor Temperature: High temperatures can degrade thrust washer performance; monitor temperature regularly to identify potential issues.
-
Use Shims: Shims can fine-tune the axial positioning of thrust washers, optimizing alignment and load distribution.
Conclusion
Thrust washers are crucial components in mechanical systems, providing support and reducing friction between rotating surfaces. Understanding their functions, types, materials, and applications is essential for engineers to design and maintain machinery efficiently and safely. By following effective strategies, tips, and tricks, engineers can optimize thrust washer performance and extend the lifespan of mechanical systems.