The Ultimate Guide to Thrust Washers: A Comprehensive Deep-Dive into Design, Applications, and Performance
Thrust washers, the unsung heroes of mechanical systems, play a pivotal role in reducing friction, mitigating wear, and ensuring optimal performance. This comprehensive guide delves into the depths of thrust washer design, applications, and performance, empowering engineers and designers with the knowledge to harness their potential effectively.
Understanding Thrust Washers
Thrust washers are thin, disk-shaped components designed to transfer axial loads between two relatively rotating or sliding surfaces. They act as sacrificial layers, dissipating energy and preventing direct metal-to-metal contact, thereby extending the lifespan of mating components.
Materials and Design Considerations
The material selection for thrust washers is crucial to their performance and longevity. Commonly used materials include:
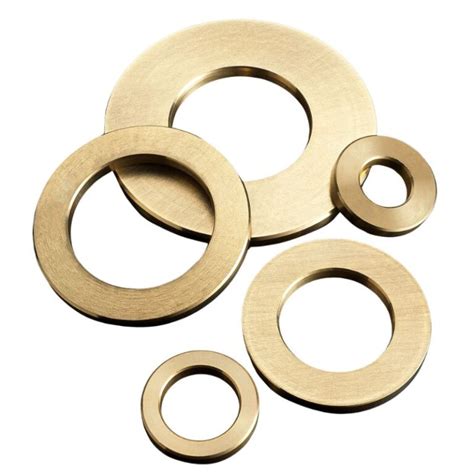
-
Bronze: Excellent wear and seizure resistance, suitable for high-speed applications
-
Steel: High strength and durability, but requires lubrication
-
PTFE Composites: Low-friction and anti-wear properties, ideal for non-lubricated environments
-
Ceramic: Exceptionally hard and wear-resistant, withstands extreme temperatures
The design of thrust washers involves several factors:
-
Thickness: Dictates the load-carrying capacity
-
Outside Diameter: Determines the contact area with mating surfaces
-
Inside Diameter: Facilitates mounting on shafts or spindles
Applications and Benefits
Thrust washers find widespread applications across various industries, including:
-
Automotive: Transmissions, clutches, and engines
-
Aerospace: Gas turbines and jet engines
-
Industrial machinery: Pumps, compressors, and rolling mills
-
Medical devices: Implantable bearings and prosthetics
Their benefits include:
-
Reduced Friction: Eliminate direct metal-to-metal contact, minimizing energy losses
-
Extended Lifespan: Protect mating components from wear and tear, prolonging their service life
-
Increased Efficiency: Enable smoother operation and reduce power consumption
-
Shock Absorption: Dampen vibrations and shock loads, minimizing noise and wear
Performance Evaluation
The performance of thrust washers is influenced by several factors:
Load Capacity: The maximum axial load that the thrust washer can withstand without failure

Wear Resistance: The ability to resist abrasive or adhesive wear under operating conditions
Friction Coefficient: Indicates the level of energy dissipation due to friction
Tables
-
Table 1: Material Properties and Applications of Thrust Washers
-
Table 2: Load Capacities of Bronze and Steel Thrust Washers
-
Table 3: Friction Coefficients of PTFE Composite Thrust Washers under Various Loads
Stories and Lessons Learned
-
Story 1: In a high-speed automotive transmission, a thrust washer failed prematurely due to insufficient lubrication. Lesson: Proper lubrication is essential to prevent overheating and wear.
-
Story 2: In an aerospace gas turbine, a thrust washer made of an incompatible material seized during operation, causing catastrophic engine damage. Lesson: Material compatibility is crucial to avoid galling and seizure.
-
Story 3: In a medical implant, a thrust washer made of PTFE composite extended the lifespan of the device by reducing friction and minimizing wear. Lesson: PTFE composites are ideal for low-friction and biocompatible applications.
Effective Strategies
-
Use High-Quality Materials: Select materials that are suited for the operating conditions and loads
-
Ensure Proper Lubrication: Lubricate thrust washers regularly to prevent wear and overheating
-
Consider Surface Treatments: Apply coatings or surface treatments to improve wear resistance and reduce friction
-
Monitor Performance Regularly: Inspect and replace thrust washers as needed to maintain optimal performance
Tips and Tricks
-
Match Thrust Washer Thickness to Load: Use thicker thrust washers for higher loads to ensure adequate support
-
Use Retainers to Prevent Movement: Install thrust washers in retainers to prevent displacement or rotation
-
Break-In Thrust Washers: Run machines at low loads initially to allow thrust washers to seat properly
Conclusion
Thrust washers are indispensable components in mechanical systems, providing essential functions such as friction reduction, wear prevention, and load distribution. Understanding their design, materials, applications, and performance is crucial for engineers and designers to optimize their use and extend the lifespan of machinery. By implementing effective strategies and following best practices, thrust washers can be leveraged to improve efficiency, reliability, and safety in a wide range of applications.