The Ultimate Guide to the PowerFlex 525 Manual: Unlocking the Power of Industrial Control
Preface
The PowerFlex 525 drive is a versatile and powerful variable frequency drive (VFD) designed for demanding industrial applications. Its intuitive user interface, robust construction, and advanced features make it an ideal choice for a wide range of industries, including manufacturing, automation, and materials handling.
This comprehensive manual provides a detailed overview of the PowerFlex 525, covering everything from installation and configuration to troubleshooting and maintenance. Whether you're a seasoned engineer or a novice technician, this guide will empower you to harness the full potential of this exceptional VFD.
Introduction to the PowerFlex 525
The PowerFlex 525 is a variable frequency drive (VFD) that controls the speed and torque of AC induction motors. It utilizes advanced pulse-width modulation (PWM) technology to provide precise and efficient motor control, resulting in improved performance, energy savings, and extended motor life.

Key Features of the PowerFlex 525
-
Versatile Power Range: Supports motors from 0.25 to 25 horsepower (0.18 to 18.5 kilowatts).
-
Wide Voltage Range: Accepts input voltages from 100 to 600 volts AC, single or three-phase.
-
IP20 Enclosure: Provides protection against dust and moisture, making it suitable for industrial environments.
-
Built-In Safety Features: Includes overcurrent, overvoltage, and undervoltage protection for enhanced safety and reliability.
-
Easy Configuration and Programming: Uses a simple programming interface with pre-defined parameter sets for various applications.
-
Advanced Communication Options: Supports multiple communication protocols, including Modbus RTU, Modbus TCP, and Profibus DP.
Benefits of Using the PowerFlex 525
The PowerFlex 525 offers numerous benefits for industrial applications:

-
Energy Savings: Optimizes motor speed and torque to reduce energy consumption by up to 30%.
-
Improved Process Control: Provides precise speed and torque control, ensuring smooth operation and enhanced productivity.
-
Extended Motor Life: Protects motors from overloads and other adverse conditions, prolonging their lifespan and reducing maintenance costs.
-
Reduced Noise and Vibration: Utilizes advanced PWM technology to minimize noise and vibration, creating a more comfortable and efficient work environment.
-
Enhanced Reliability: Features a robust design and built-in safety features to ensure reliable operation in demanding industrial environments.
Installation and Configuration
Installation Considerations
Before installing the PowerFlex 525, it is essential to consider the following factors:
-
Mounting: Mount the VFD on a vertical surface, ensuring adequate ventilation and accessibility.
-
Wiring: Connect the VFD to the power source, motor, and control devices following the manufacturer's instructions.
-
Grounding: Properly ground the VFD and all connected equipment to prevent electrical hazards.
-
Safety Precautions: Wear appropriate personal protective equipment (PPE) and follow all safety guidelines during installation.
Configuration Parameters
The PowerFlex 525 allows users to customize its operation through the following configurable parameters:
-
Motor Control Parameters: Adjust motor speed, torque, and acceleration/deceleration rates.
-
Input/Output Parameters: Configure analog and digital inputs/outputs for control and monitoring.
-
Communication Parameters: Set up communication protocols for remote access and monitoring.
-
Safety Parameters: Enable and adjust safety features such as overcurrent and undervoltage protection.
Factory Default Settings: The PowerFlex 525 comes pre-programmed with factory default settings for various applications. These settings can be modified to meet the specific requirements of each installation.
Troubleshooting and Maintenance
Common Troubleshooting Issues
The PowerFlex 525 provides diagnostic capabilities to help troubleshoot common issues:

-
Power Faults: Check for loose connections, power supply issues, or tripped circuit breakers.
-
Motor Faults: Inspect the motor for mechanical problems or electrical faults.
-
Communication Faults: Verify correct communication settings and cable connections.
-
Overheating: Ensure proper ventilation and check for excessive load or environmental factors.
-
Error Codes: The VFD displays error codes to indicate specific faults or conditions. Refer to the manual for error code explanations.
Preventative Maintenance
Regular maintenance helps ensure the optimal performance and longevity of the PowerFlex 525:
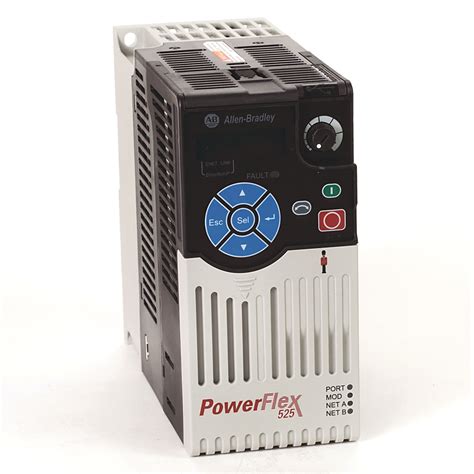
-
Periodic Inspections: Inspect the VFD for dust, dirt, or loose connections.
-
Cleaning: Clean the VFD using a damp cloth and avoid using harsh chemicals or solvents.
-
Software Updates: Download and install software updates from Rockwell Automation to improve functionality and address potential issues.
-
Capacitor Replacement: Electrolytic capacitors may require replacement after several years of operation. Refer to the manufacturer's recommendations for replacement intervals.
-
Environmental Conditions: Maintain a clean and well-ventilated environment around the VFD to prevent overheating and premature failure.
Case Studies and Best Practices
Case Study 1: Energy Savings in a Manufacturing Plant
A manufacturing plant installed the PowerFlex 525 VFDs to control the speed of their conveyor motors. By optimizing the speed of the conveyors based on actual production needs, they achieved energy savings of up to 30%, resulting in significant cost reductions and a reduced carbon footprint.
Case Study 2: Improved Process Control in a Food Processing Facility
A food processing facility used the PowerFlex 525 to precisely control the speed of their slicing machines. This resulted in consistent slice thickness, reduced product waste, and increased overall production efficiency. The precise speed control also ensured food safety by preventing uneven slicing, which could lead to contamination.
Case Study 3: Extended Motor Life in a Mining Operation
A mining operation installed the PowerFlex 525 to control the speed and torque of their ventilation fans. The VFD's robust construction and advanced safety features protected the motors from harsh environmental conditions and sudden load changes. As a result, the motors experienced significantly extended lifespans, reducing maintenance costs and downtime.
Effective Strategies for Using the PowerFlex 525
Energy Management
-
Use Variable Speed Control: Adjust motor speed to match actual load requirements, reducing energy consumption.
-
Enable Energy Savings Mode: Activate the VFD's energy-saving features to further optimize energy efficiency.
-
Monitor Energy Usage: Utilize the VFD's monitoring capabilities to track energy consumption and identify areas for improvement.
Process Optimization
-
Maintain Accurate Speed Control: Utilize the VFD's precise speed control capabilities to ensure optimal process efficiency.
-
Implement Programmable Logic: Use the VFD's built-in PLC functionality to create custom logic for specific application requirements.
-
Minimize Noise and Vibration: Configure the VFD to reduce motor noise and vibration, creating a more comfortable work environment.
Maintenance and Reliability
-
Follow Preventative Maintenance Schedule: Adhere to the manufacturer's recommended maintenance intervals to prevent unexpected failures.
-
Use Diagnostic Tools: Utilize the VFD's diagnostic capabilities to identify and troubleshoot potential issues early on.
-
Upgrade to Latest Software: Keep the VFD software up to date to benefit from the latest features and improvements.
Tips and Tricks for Success
-
Attend Training Workshops: Participate in Rockwell Automation training programs to gain hands-on experience with the PowerFlex 525.
-
Consult with Experts: Reach out to Rockwell Automation support engineers or authorized distributors for technical advice and troubleshooting assistance.
-
Join Online Forums: Engage with other PowerFlex users and experts in online forums to share knowledge and best practices.
-
Use Simulation Tools: Utilize Rockwell Automation simulation software, such as RSLogix Emulate 500, to test and verify your configurations before implementing them in the field.
-
Document Your System: Create detailed documentation of your PowerFlex 525 installation, including wiring diagrams, parameter settings, and maintenance records.
Conclusion
The PowerFlex 525 variable frequency drive is a powerful tool that can significantly improve the performance, efficiency, and reliability of industrial applications. By understanding the principles of operation, proper installation and configuration, and effective troubleshooting and maintenance techniques, you can unlock the full potential of this exceptional VFD.
Remember, by embracing the strategies, tips, and tricks outlined in this guide, you can maximize the benefits of the PowerFlex 525 and achieve optimal outcomes in your industrial operations.
Tables
Table 1: PowerFlex 525 Specifications
Specification |
Value |
Power Range |
0.25 to 25 horsepower (0.18 to 18.5 kilowatts) |
Input Voltage Range |
100 to 600 volts AC, single or three-phase |
Output Frequency Range |
0 to 650 hertz |
Overload Capacity |
150% for one minute, 200% for 3 seconds |
Enclosure Rating |
IP20 |
Communication Protocols |
Modbus RTU, Modbus TCP, Profibus DP |
Table 2: Common Troubleshooting Codes
Error Code |
Description |
AL |
Alarm |
OL |
Overload |
UF |
Underfrequency |
OV |
Overvoltage |
GF |
Ground Fault |
**Table 3: